Context
An independent company working in the railways since 1 April 2015 wanted to adopt a new way of managing its 600 employees by the implementation of "continuous improvement”.
Objectives
To implement this new culture, two operational pilot projects were launched:
- Maximize cleanliness in the train
- Ensure the punctuality of trains from Paris
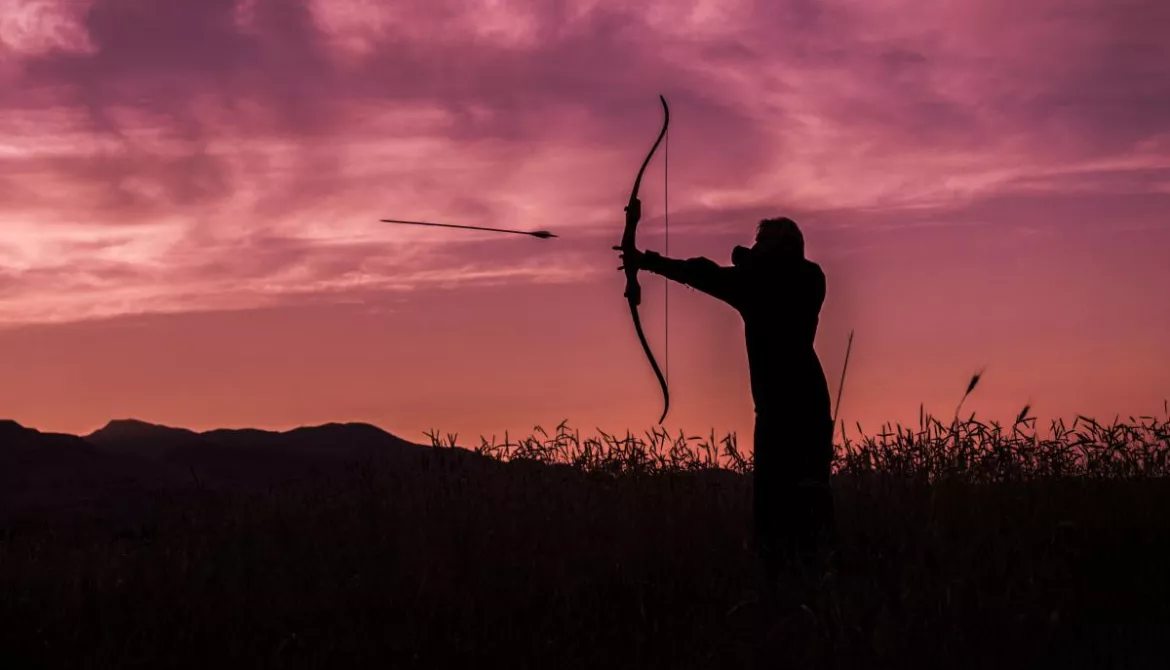
Our Approach
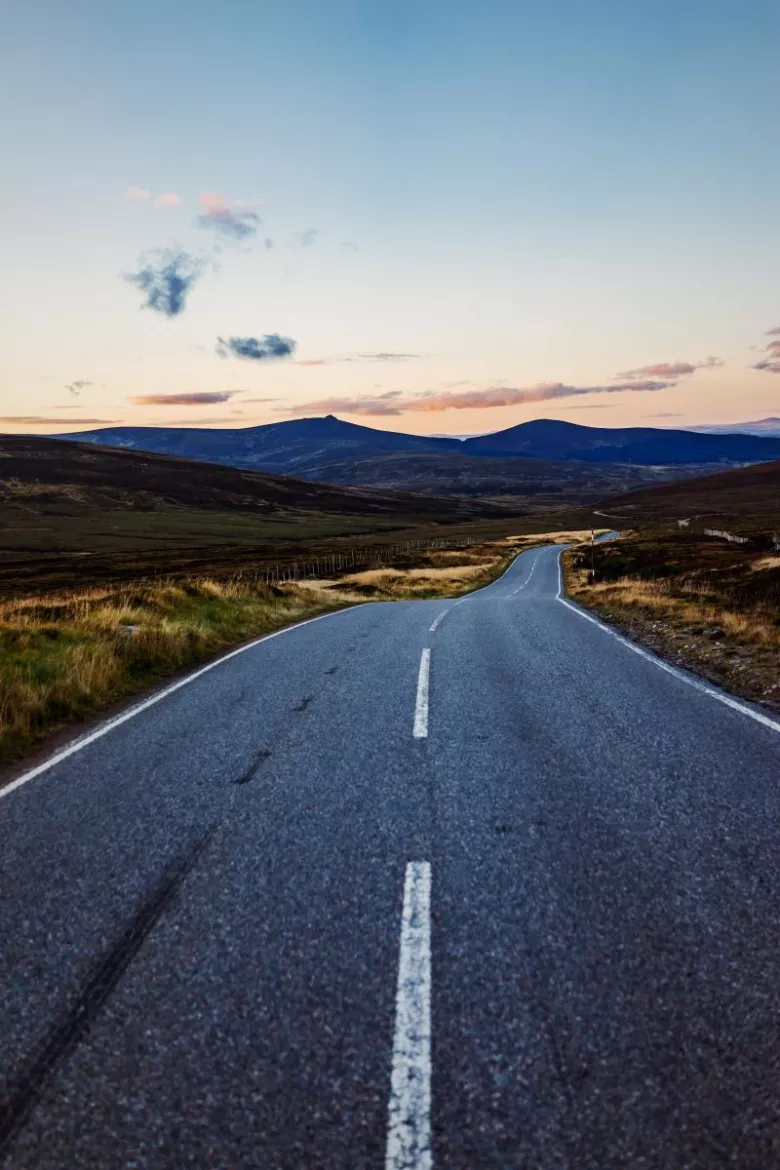
A mixture of a “pure” operational excellence approach with a line change approach divided into 5 areas:
- Raise awareness of the Executive Committee on two sessions with practical exercises, a presentation of best practices and Gemba
- Use of LEAN methodology for both pilot projects including the search for "quick wins”
- Train managers
- Train 40 line managers
The Operational Excellence and LEAN methodology:
- Approach Change management/communication will impact 600 employees
Results
- Improved cleanliness and punctuality
- Presence of LEAN skills at the customer and use as part of the initiation and monitoring of future projects
- Exemplary role of management regarding Operational Excellence Continuous Improvement
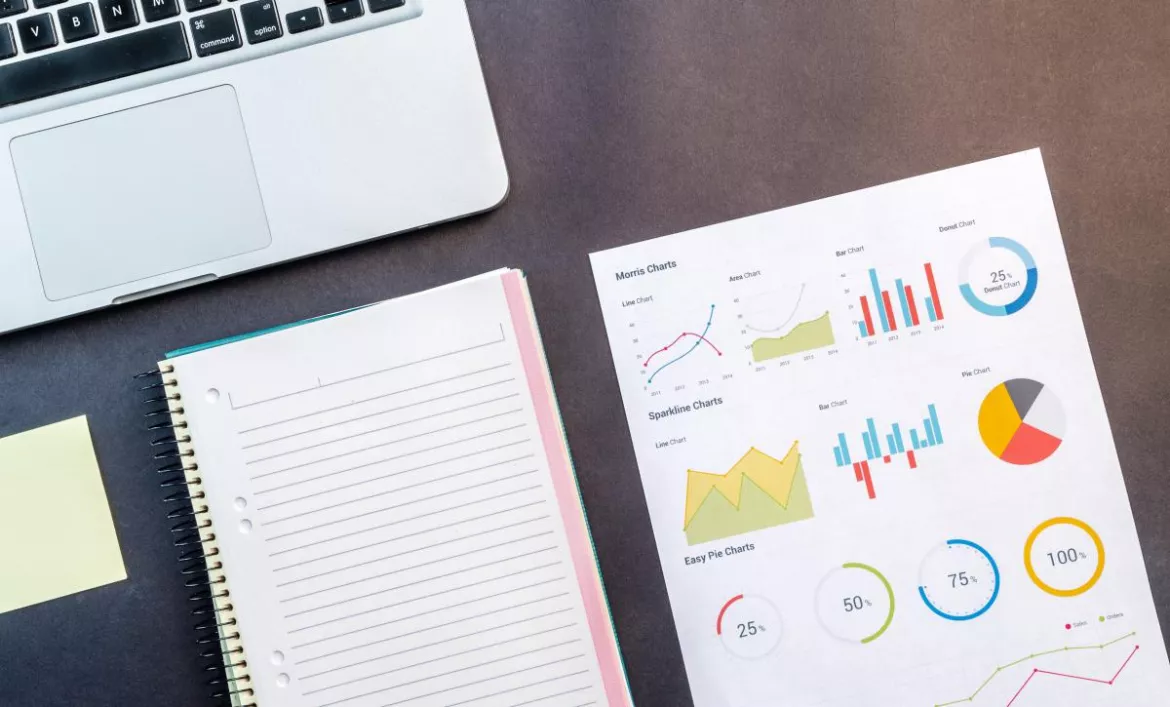