Context
A major pharmaceutical company had launched a global program to streamline its efficiency "more with less"
Objectives
- The key objective was to increase productivity in the visual inspection department. The key metric was the number of doses inspected per FTE
- Challenge: "45% AVI volume increase in 2016 would require xxx new FTEs w/o productivity gains; however this creates a gap of xxx FTEs with Dec 2016 budget"
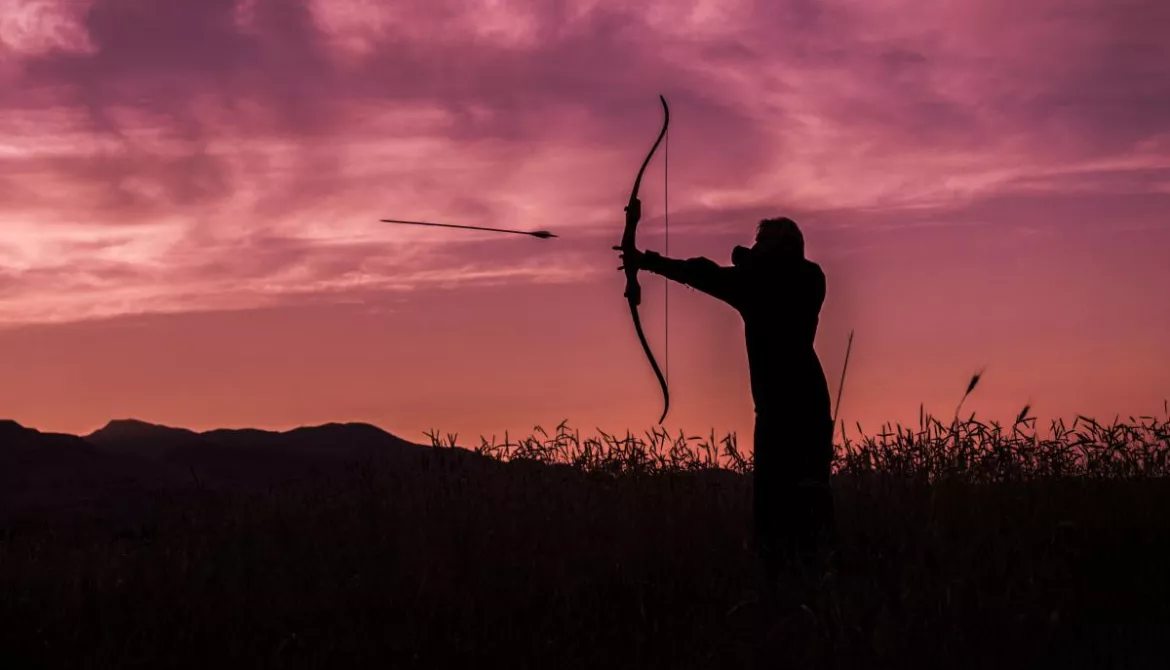
Our Approach
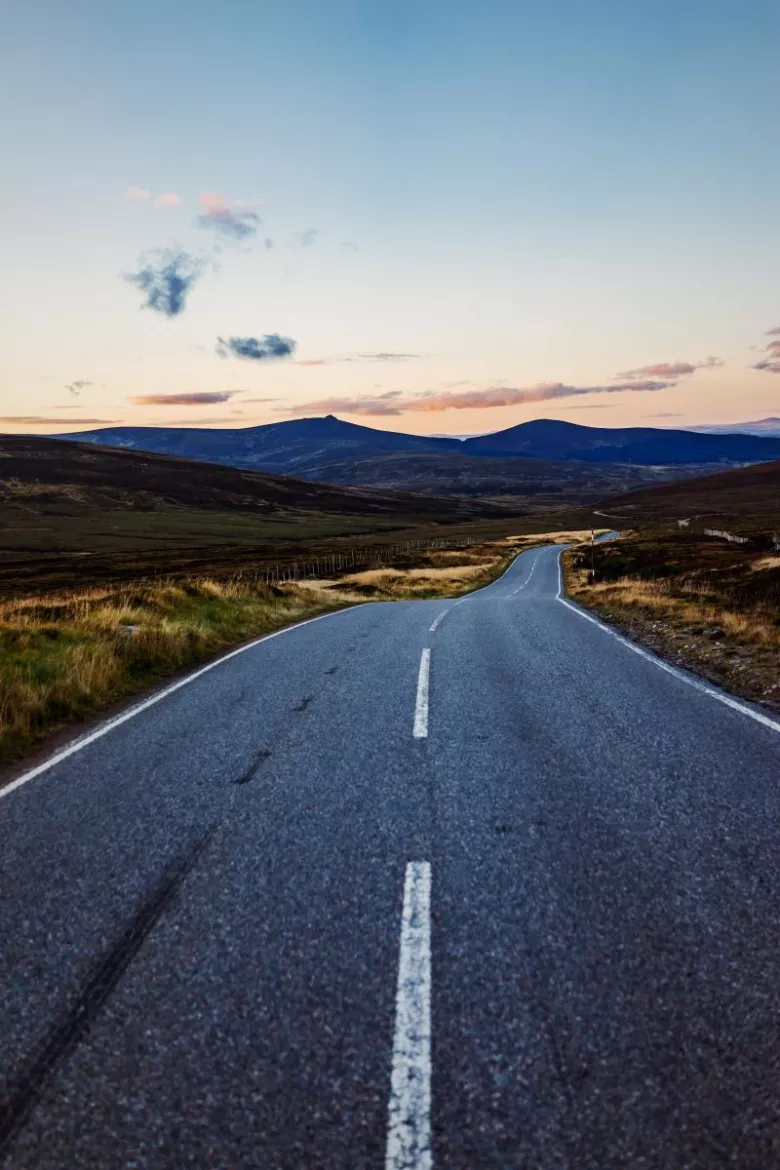
- Conducted diagnostic to identify levers and estimate potential savings:
- Organization of workshop to identify potential levers and align with experts on what analysis to be conducted to estimate the size of potential gains
- Conducted 1-to-1 interviews with cross-functional teams (eg. Production, quality, logistics, maintenance, etc...) to estimate effort and timings for implementation
- Identification of 14 levers and prioritization in terms of impact vs effort/timing
- Identification of 7 levers selected for implementation
- Implemented 7 prioritized levers
- Estimate gains (levers) performed while taking into account interdependencies between different levers
Results
- Resulted in productivity gains of 27%
- Department maintained the same levels of production with a reduction of 38 FTEs
- Recurrent annual cost saving of € 2.8M
- Therefore the department will be capable of handling higher volumes with fewer FTEs
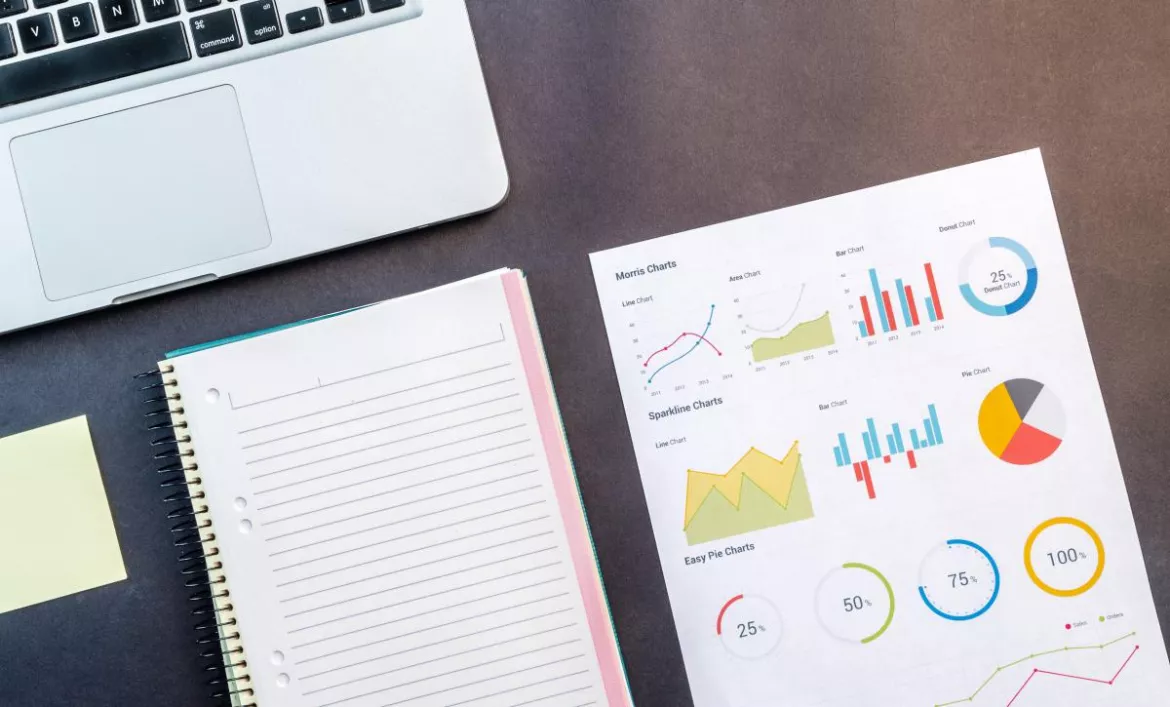